The concepts surrounding ‘lean thinking’ and the elimination of ‘wastes’ originated in the manufacturing industry – more specifically, in the auto industry. The term lean thinking was originally coined by James P. Womack and Daniel T. Jonesin their 1991 book ‘The Machine That Changed the World’ which focused on Toyota’s production system and the concepts have been used by manufacturers worldwide since that time to improve production and efficiency.
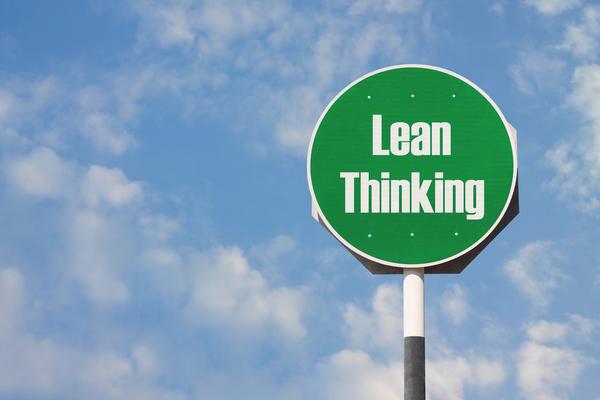
But every business – no matter what industry – has room for improvement. There are undoubtedly places in your company where you’re misusing resources or where time or money is being wasted. And that means that the concepts behind lean thinking can probably help your office improve too. There’s always a better way to do things.
1. Clear, measurable goals
Lean thinking helps teams establish and concentrate on measurable goals and metrics whether those are improved sales numbers or reductions in lost-time injuries. By having your leadership team commit to a particular goal and focus on it (posted visuals and progress charts help), your employees can pull together and move in the same direction towards what’s most important.
2. Streamlined processes
Do you have multiple employees in your office who complete the same task? Chances are, they do that task differently and some of them probably work more effectively than others. Personal preferences and work behaviours – rather than objective facts – often drive processes. By establishing clear steps and standards for how things should be done, you’ll create efficiencies and improve processes for the whole team.
3. Clutter reduction
Paper clutter is a major problem for most businesses. Searching for documents wastes time and adds stress and frustration to the workplace, and mishandled paperwork detracts from your ability to provide outstanding value to your customers. Examine your information management systems across departments and see where you could better organise paper documents– or maybe eliminate them altogether by putting them in a central location in the cloud.
4. Resource allocation
Improved resource allocation involves assigning and allocating budget, equipment, tools, people and information to the areas where they’re needed most. By cutting out waste and improving resource allocation, you’ll be able to gather data more quickly, make faster decisions and improve delivery to customers.
5. Cross-training
How often have you been stuck or lost time because the one person who knew the answer – or how to use the software or where to find the information – was out of the office or left your company? Incidents like these not only waste time and money but also hurt customer service. By setting up effective cross-training and succession planning programs, you’ll ensure that all your teams function more efficiently.
Need help in analysing your workplace and implementing lean thinking practices? Contact the expects at your local Accru office today.